top of page
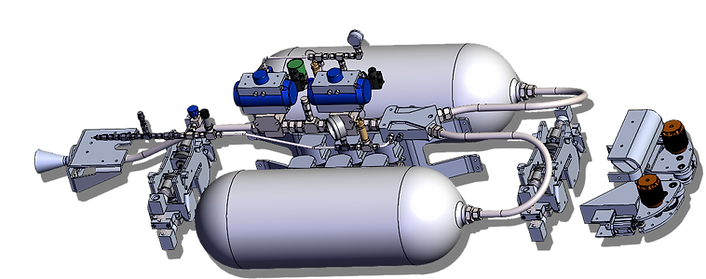
pod v
design
STATS
3500
N PEAK THRUST
265
MPH TOP SPEED
7
G'S OF DECELERATION
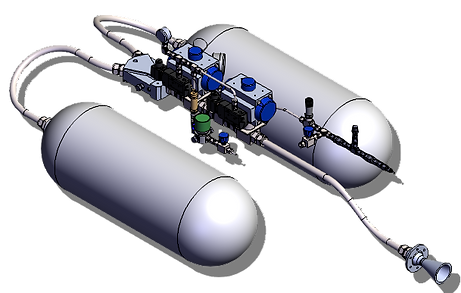
PROPULSION SYSTEM
The objective of the propulsion system is to reach the fastest speed possible on a one mile long track. In order to accomplish this, the thrust for the pod is produced via energy stored in the form of compressed nitrogen gas inside two composite overwrapped pressure vessels (COPVs). The flow of nitrogen from each vessel converges in the manifold and is accelerated to supersonic speeds through the nozzle for maximum thrust.
To safely bring the pod to a stop, the braking system was designed with reliability and power in mind. To stop from a top speed of 300 mph, 12 custom-designed pistons activate at 150 psi to create over 5000 pounds of actuation force, achieving a braking force of 7 g’s. Powering the system is a complex pneumatic assembly that operates even in critical mission failure to stop the pod in a controlled manner.
BRAKING SYSTEM


E - DRIVE SYSTEM
After optimizing the potential of our cold gas thruster, the team looked toward other ways to improve the pod’s performance. Research led to the advantages of an electric motor at low speeds with high torque. The E-drive acts as an initial propulsion system to bump up the pod's velocity before switching over to the cold gas thruster for maximum speed. The design features two pneumatic actuating gear boxes that drive wheels powered by electric motors. Theoretically it could get the pod to 50 mph.
In order to ensure pod alignment along the I-beam, stability utilizes a system of wheels, linkages, and springs to remain steady under acceleration and braking. In addition, stability mitigates the effects of bumps or irregularities in the track such that the pod has a smooth and controlled ride.

STABILITY SYSTEM

THE CHASSIS
To assist weight savings while ensuring strength and rigidity, the chassis is made of composite sandwich paneling with a honeycomb core. The pod's other subsystems are attached to the chassis via hardpoints.
We use a custom PCB serves as the controls module for the pod. It controls the microcontroller, sensor boards, ethernet shields, and other components.

POWER AND CONTROL
bottom of page